Injection Molding & RIM
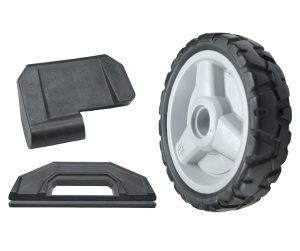
Peridot offers comprehensive assistance in every stage of the injection molding process, from designing prototypes to full-scale production. With their expertise in injection molding techniques, Peridot can effectively optimize the design of prototypes to ensure they meet the desired specifications and functionality. Their skilled team can help clients refine their concepts and create 3D models for thorough evaluation before moving to production. Peridot’s one-of-a-kind facility and advanced technologies ensure efficient and cost-effective production of high-quality injection-molded parts. By leveraging their services, businesses can benefit from a streamlined process that minimizes time-to-market and maximizes product performance. Whether it’s a small-batch run or large-volume production, Peridot is a reliable partner to guide clients from initial design to successful end production.
Injection Molding
Injection molding is a widely used manufacturing process that involves injecting molten material, typically plastic, into a mold cavity to create complex and precise 3D objects. This versatile technique offers high production efficiency, consistency, and cost-effectiveness, making it a preferred choice for mass-producing plastic parts. The process starts with the raw material being fed into a heated barrel, where it is melted before being forced into the mold under high pressure. Once the material cools and solidifies, the mold is opened, and the finished product is ejected. Injection molding is invaluable in various industries, including automotive, electronics, and consumer goods, for its ability to produce high-quality and custom-made components in large volumes.
We offer complete:
Concept and design services
Engineering consultation and support
Product development, including prototyping
Material selection
Fabrication capabilities in both plastic and rubber
Value-added services, such as assembly
- Acetal
- ABS
- Nylon
- Kepital
- TPV
- & MORE
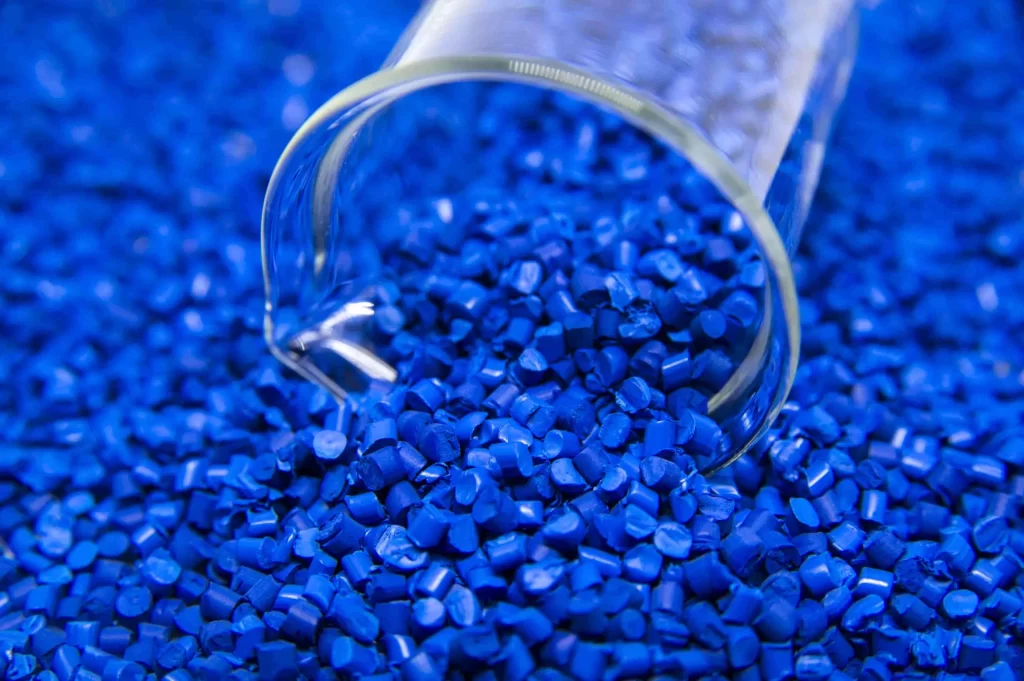
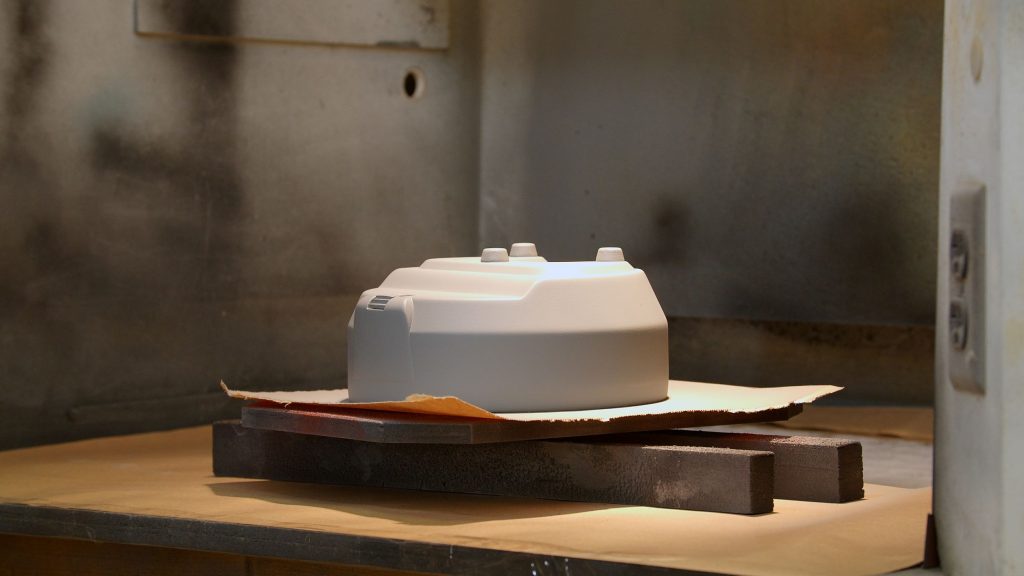
Polymer Molding / RIM
Reaction Injection Molding (RIM) is an innovative manufacturing process that involves combining two liquid components, typically polyurethane-based materials, within a mold cavity. The mixture undergoes a chemical reaction, causing it to expand and fill the mold. RIM offers numerous advantages, including cost-effectiveness, fast cycle times, and the ability to create large and complex parts with excellent surface finishes. This technique is particularly well-suited for producing lightweight, durable, and impact-resistant components. RIM molding finds widespread application in industries like automotive, electronics, and medical devices, where high-quality and precision parts are essential for success. Embracing RIM molding enables businesses to efficiently manufacture high-performance products while meeting the demands of modern manufacturing challenges. Utilizing 3D printed master patterns in RIM molding revolutionizes manufacturing efficiency, as these precision-engineered templates streamline the production process. With these innovative 3D printed masters, Peridot can achieve unparalleled accuracy and cost-effectiveness in their RIM molding operations.