Additive Manufacturing
Additive Manufacturing
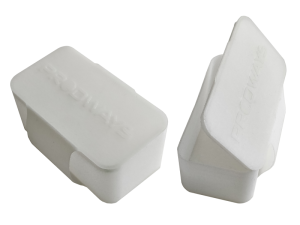
NEW - Selective Laser Sintering - High Temp
With the addition of a high temperature SLS process, Peridot can now offer the full breadth of materials associated with this technology platform. Currently, Peridot is utilizing this platform to run the PA12-CF material.Printing with PA12-CF, or carbon fiber-reinforced polyamide 12, offers numerous advantages that make it a sought-after material for additive manufacturing applications. PA12-CF combines the exceptional properties of carbon fiber with the versatility of polyamide 12, resulting in enhanced mechanical strength, stiffness, and heat resistance. This combination makes PA12-CF an ideal choice for producing lightweight yet robust parts that can withstand high-stress environments. The material’s low coefficient of thermal expansion and excellent dimensional stability further contribute to its appeal. PA12-CF’s ability to reduce warping and shrinkage during the printing process ensures greater accuracy and consistency in the final product. Additionally, its corrosion resistance and electrical conductivity make it suitable for a wide range of industries, including automotive, aerospace, and consumer electronics. Embracing PA12-CF for additive manufacturing enables businesses to achieve superior performance and durability in their 3D-printed components, meeting the demands of modern engineering and design challenges.
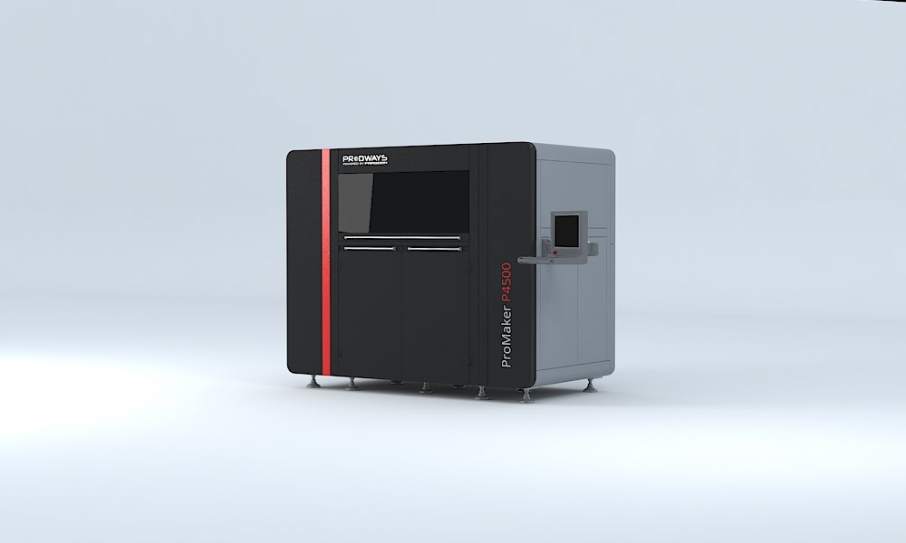
Applications
- Under hood engine components
- Rapid tooling applications
- Wind tunnel model testing
Materials
Selective Laser Sintering
Selective Laser Sintering (SLS) is a cutting-edge additive manufacturing process that uses a high-powered laser to fuse powdered materials into 3D objects. In SLS, a bed of powdered material, such as polymers or metals, is evenly spread, and the laser selectively sinters the particles together based on the CAD model’s cross-section. The process is repeated layer by layer until the final object is created. SLS offers exceptional material versatility, enabling the production of functional prototypes, complex geometries, and even end-use parts. Its ability to work with a wide range of thermoplastics and metal powders makes it a preferred choice in industries like aerospace, automotive, and healthcare. With Selective Laser Sintering, manufacturers can achieve high accuracy, intricate designs, and rapid production, revolutionizing the world of additive manufacturing.
Applications
- Living Hinges
- Form, Fit, and Concept Models
- Housings & Enclosures
- Snap-Fit Joints
- Performance Testing
- Complex Geometries
Materials
- PP1400 - BLACK Polypropylene
- PA12 - Carbon Filled
- PA11-GB30 - Natural
- PA11-Black
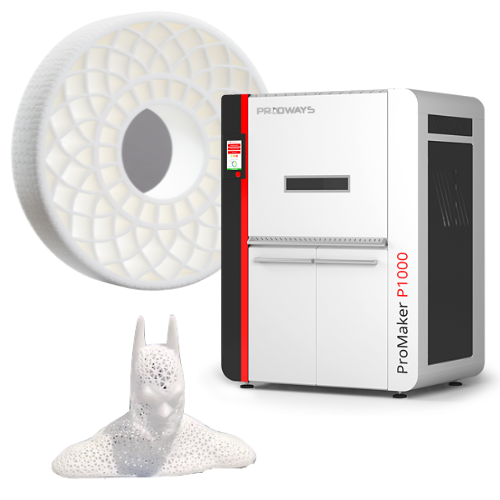
PERIDOT was one of the initial world launch sites for BASF’s new PP1400 polypropylene material.
Producing not only prototypes but focusing on higher quantity production-level components using this additive manufacturing process.
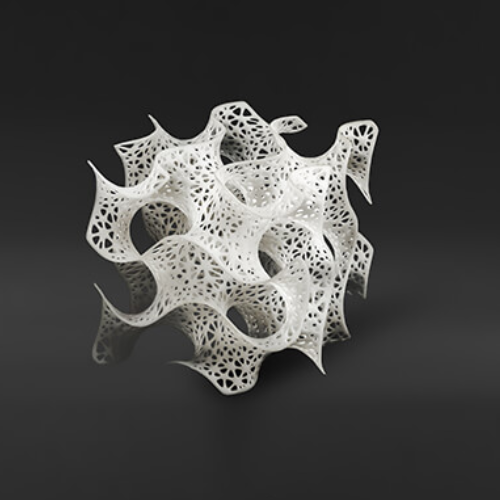
Stereolithography
Stereolithography, also known as SLA 3D printing, is an advanced additive manufacturing process that utilizes photopolymerization to create high-resolution 3D objects. In this technique, a liquid resin, often referred to as photopolymer, is exposed to ultraviolet (UV) light in a layer-by-layer manner, causing the resin to solidify and form the desired object. SLA offers exceptional precision and accuracy, making it perfect for producing intricate prototypes, architectural models, and custom components. Its ability to create complex geometries with fine details sets it apart as a top choice in the additive manufacturing industry. With the growing demand for rapid prototyping and custom manufacturing solutions, stereolithography proves to be an invaluable tool for various sectors seeking efficient and precise 3D printing capabilities.
Applications
- Living Hinges
- Form, Fit, and Concept Models
- Housings & Enclosures
- Snap-Fit Joints
- Performance Testing
- Complex Geometries
Materials
Fused Filament Fabrication
Fused Filament Fabrication (FFF), also known as Fused Deposition Modeling (FDM), is a popular additive manufacturing process widely used for 3D printing. In FFF, a thermoplastic filament is fed through a heated nozzle, which melts the material into a semi-liquid state. The nozzle moves in a controlled manner, depositing the melted filament layer by layer to build the 3D object. FFF is renowned for its simplicity, cost-effectiveness, and accessibility, making it a preferred choice for hobbyists, engineers, and businesses alike. Its ability to produce functional prototypes, concept models, and end-use parts with a wide range of thermoplastic materials adds to its versatility. With Fused Filament Fabrication, users can efficiently and affordably create custom 3D printed objects, catering to various needs and applications across different industries.
Applications
- Form, Fit, and Concept Models
- Enclosures
- Jigs & Fixtures
- Performance Testing
- Complex Geometries
Materials
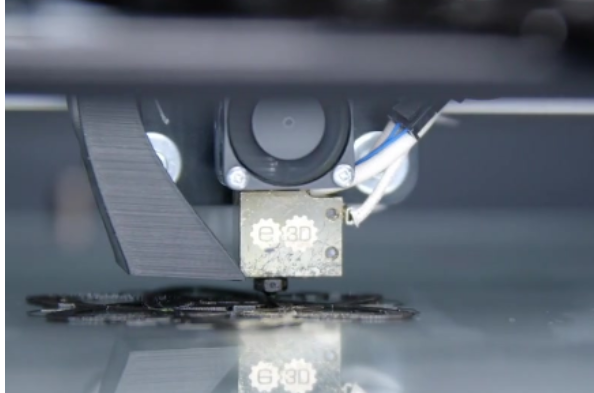